The U.S. government has taken significant steps to bolster research into digital twin technology within the semiconductor industry. This move comes amidst growing recognition of the potential benefits that digital twin systems can offer in enhancing the efficiency and productivity of semiconductor manufacturing processes.
Digital twin technology involves creating a virtual replica or representation of physical assets, systems, or processes. In the context of the semiconductor industry, digital twins can mimic the behavior and performance of manufacturing equipment, such as lithography machines and wafer fabrication tools, enabling manufacturers to simulate and optimize their operations in a virtual environment.
By funding research initiatives focused on digital twin technology in the semiconductor sector, the U.S. government aims to drive innovations that can improve the overall competitiveness and sustainability of the industry. Digital twins have the potential to revolutionize the way semiconductor manufacturers design, test, and optimize their production processes, leading to faster time-to-market, higher product quality, and reduced costs.
One key area of focus for digital twin research in semiconductors is the development of sophisticated modeling and simulation algorithms that can accurately replicate the complex interactions and dynamics of semiconductor manufacturing processes. These models enable engineers and operators to predict and prevent potential issues, optimize process parameters, and identify opportunities for efficiency improvements.
Moreover, digital twins can facilitate enhanced monitoring and control of semiconductor manufacturing operations in real-time. By integrating sensor data, machine learning algorithms, and advanced analytics, digital twin systems can provide valuable insights into equipment performance, process variations, and production bottlenecks, enabling manufacturers to make data-driven decisions and optimize their operations for maximum efficiency.
Furthermore, digital twins can support the implementation of predictive maintenance strategies in semiconductor manufacturing facilities. By continuously monitoring the health and performance of equipment through the virtual twin models, manufacturers can proactively identify maintenance needs, schedule interventions, and minimize unplanned downtime, leading to improved equipment reliability and longevity.
In conclusion, the U.S. government’s support for digital twin research in the semiconductor industry underscores the importance of leveraging advanced technologies to drive innovation and competitiveness. By investing in the development of digital twin systems, semiconductor manufacturers can unlock new opportunities for optimizing their operations, improving product quality, and maintaining a competitive edge in the global marketplace. As digital twin technology continues to evolve and mature, its potential to transform the semiconductor industry remains promising, paving the way for a more efficient, agile, and sustainable manufacturing ecosystem.
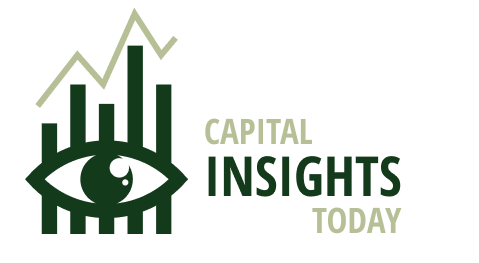